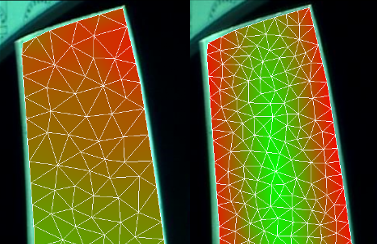
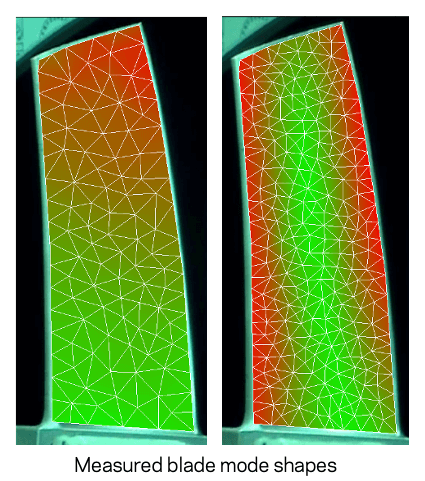
Gas-turbine engines provide a large percentage of the electricity used around the world. The turbine blades that deliver the shaft power to generators must be able to withstand high mechanical stress, extreme heat, and unsteady aerodynamic forces. Under some circumstances, a self-excited aeroelastic instability—termed flutter—can occur. Flutter is the result of a non-linear coupling between blade vibration and aerodynamic forces. Understanding the conditions that can cause flutter for a specific turbine design is a critical part of engine development.
The Notre Dame Turbomachinery Laboratory (NDTL), in collaboration with Doosan Heavy Industries & Construction Co. Ltd. (DHI), recently conducted a successful test campaign to investigate flutter in a fully three-dimensional, high-speed, annular turbine cascade. Careful design of inflow and exit conditions provided the blades with engine-relevant flow conditions. The experiments used blades that were mechanically actuated at the natural frequencies in order to simulate the real three-dimensional mode deflection shapes that would be observed in the rotating turbine. Measurements of steady and unsteady pressures on the blades provided the critical data required to understand the conditions that could lead to flutter.
Inquiries can be sent to ndturbo@nd.edu.
By Jeongseek Kang
Published by Jasmin Avila