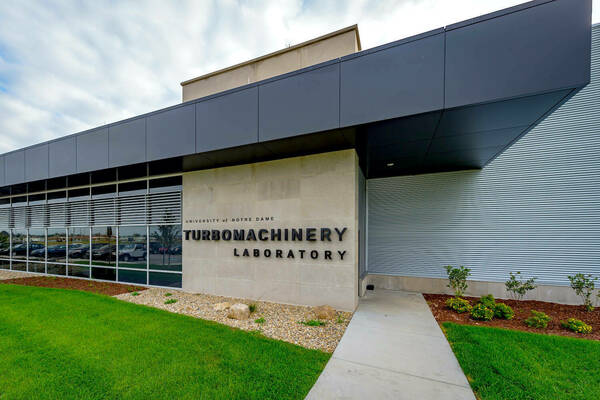
The Notre Dame Turbomachinery Laboratory (NDTL) and Jetoptera recently partnered to conduct a Small Business Technology Transfer (STTR) proof-of-concept (Phase I) study of Jetoptera's Fluid Propulsive System Thruster. The Fluid Propulsive System (FPS™) is a novel architecture that uses a source of compressed air to produce thrust. The FPS™ is a patented, scalable means to power a range of aircraft for both VTOL and STOL applications.
"We compared the FPS™ and three other legacy propulsion technologies for Vertical Take Off and Landing (VTOL) UAVs and UAM vehicles on the same power supply basis. With the help of the exceptionally skilled personnel at the Notre Dame Turbomachinery Laboratory and using their modern facilities and data reduction techniques, we measured, analyzed, and confirmed the FPS™ lower noise emissions potential versus legacy systems," said Dr. Andrei Evulet, CEO of Jetoptera, Inc. NDTL and Jetoptera collaborated to design a test matrix that would confirm and deepen understanding of findings from previous investigations.
Experiments were conducted in the Anechoic Wind Tunnel (AWT) Facility at the Hessert Laboratory for Aerospace Research at the University of Notre Dame. NDTL engineers and technicians designed and constructed a hemispherical 25-microphone array for the acoustic measurements in the AWT and installed a custom compressed air delivery system to supply the thrusters with motive flow. Additionally, the NDTL team designed and implemented a custom 1-D force balance for measuring the aerodynamic performance of the test articles.
With this test setup, the NDTL-Jetoptera team successfully characterized the aero performance and acoustics signature of the FPS™, information vital to the development of the FPS™ technology.
By Mark H. Ross
Published by Jasmin Avila-Sacco